Fulfillment knowledge
Initial inventory and goods receipt inspection
Why your article doesn't get in here so easily - about the importance of a meticulously conducted initial inventory and a clean incoming goods inspection
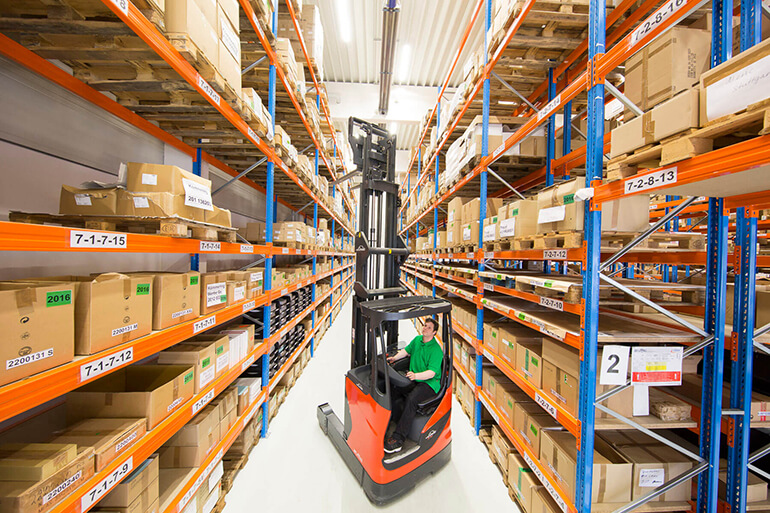
If we are allowed to win a new partner for us, an initial inventory is carried out
For the benefit of all parties, a detailed initial inventory as well as an accurate incoming goods inspection later on are an absolute must. Anyone who is allowed to store and ship products, printed matter or advertising materials for a partner wants clear conditions - for both sides. A shared understanding of the initial situation lays the foundation for further work. A first "getting to know" of all items included - now we can start! Therefore, we spend sufficient time and effort on these two process steps....
Initial inventory If we are allowed to win a new partner for us, an initial inventory is carried out. All articles (SKU's - Stock keeping Units) are recorded individually. Article number, description. The individual articles are weighed and the so-called "master data" is created.
The following steps are carried out:
→ Determination whether single item and packaging unit.
→ Determination of the SKU (Stock Keeping Unit). Unique article number.
→ Determination of the weight of the article, respectively the shipping unit.
→ Geo-data determination: length x height x width of the article / the shipping unit => this results in the maximum floor space of the article.
base area of the article. This is important for the subsequent determination of the outer packaging.
→ Quantity of the article / shipping unit
→ Entry of the supplier / scan of this delivery bill to SKU
→ Assignment of the pallet location number / manual rack number, depending on the storage technology.
→ Printout and application of the label with the SKU of the article. This is as a barcode and in plain text on the label.
→ Notification to responsible project manager
→ After the initial notification to the customer, there may be a few rounds of reconciliation, depending on whether the determined
→ quantities correspond to the delivery bills, or there are items that were not notified in advance. This takes place in
intensive coordination between the customer and the project manager.
After approval by the project manager in coordination with the customer, the new warehouse is set to "productive". I.e. from now on, shipping can begin.
Running goods receipt The goods receiving department has the most important function in the Pick & Pack process. Here the course is set for further processing. The following checks are carried out and the associated information is recorded:
→ Quantitative and qualitative incoming goods inspection.
→ Reporting of any qualitative defects or quantitative deviations max. 3 percent.
→ Determination whether single item and packaging unit
→ Determination of SKU (Stock Keeping Unit). Unique item number.
→ Determination of the weight of the article, respectively the shipping unit.
→ Geo-data determination: length x height x width of the article / the shipping unit => this results in the maximum
base area of the article. This is important for the subsequent determination of the outer packaging.
→ Quantity of the article / shipping unit
→ Entry of the supplier / scan of this delivery bill to SKU
→ Assignment of the pallet location number / manual rack number, depending on the storage technology.
→ Printout and application of the label with the SKU of the article. This is as a barcode and in plain text on the label.
→ Message to responsible project manager
→ The recording of this data serves as the basis for further Pick & Pack.
The aim here is to update the article master data and to serve as a data basis for the further shipping processes.