Fulfillment knowledge
Pick & Pack - Core Element of Fulfillment
Hardly any element of modern fulfillment has such significance as the pick & pack process. Highly efficient, IT-supported processes accompany people in their daily work. Nevertheless, the human factor is an essential part of this process. IT support massively increases efficiency while eliminating sources of error.
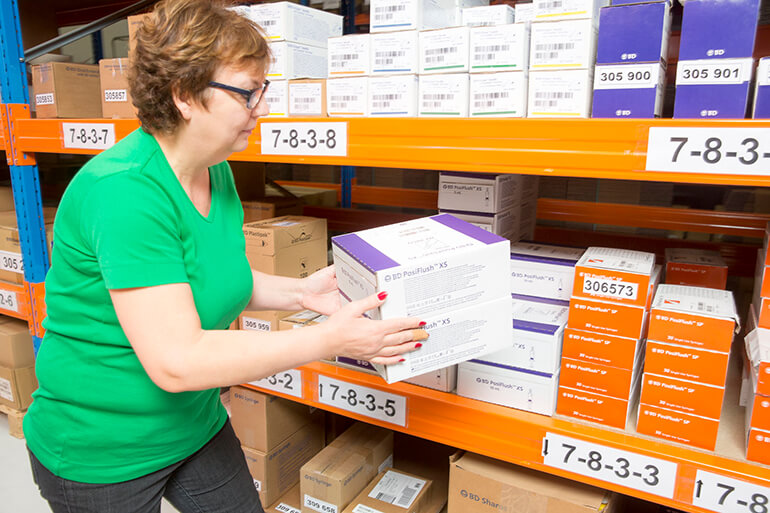
Pick & Pack is the heart of fulfillment, so to speak
Pick Each shipping order received generates a delivery bill (which is enclosed with the shipment) or a picking bill if the shipment is delivered without a delivery bill. The respective document contains the delivery note number as a barcode. So basically there is always a document with a barcode printed on it. In our case, this looks like this, for example. Lieferscheinnummer: 322-04711893.
Central element of the picking process are two components:
-
route optimization: The merchandise management system always knows exactly where which item is located. That is, on which storage location or shelf. In route optimization, the aim is to minimize or optimize the distance from one picking part to the next, i.e. the article (SKU). The "Traveling Salesman Problem" is a classic problem in the theory of route optimization. It is based on the assumption that different target points should be reached only once within a cycle with a minimum time span. To solve this problem, the path lengths of all possible walking routes can be calculated and then the one with the smallest path length, considering the available resources, can be selected.
-
rearrangement: A very practical problem. Articles, i.e. SKU's, which are often used, should be in a high-bay warehouse at the ready-to-hand places, as accessible up to two meters. This is so that the personnel can carry out the picking process as quickly as possible. The merchandise management system permanently analyzes the outflow of articles and provides the warehouse personnel with important tips for relocating articles from higher storage regions to regions that are directly accessible to the picking personnel. So, for example, if an item goes out of stock more than at an earlier point in time due to seasonal aspects, staff are advised to store this item ready to hand. Other items can be put back at the top of the high-bay warehouse due to less runoff. The challenge of the algorithm is to recognize whether these are short-term effects that lead to this material outflow (e.g. trade fairs), or whether these are longer-term aspects, such as seasonal effects.
& Pack The individual components (items) of the order are placed in a suitable outer packaging at the point-of-pack (PoP). The appropriate outer packaging is suggested to the employee by the merchandise management system. Due to the geo-data entry at goods receipt, all information of the order and its contents are available. The SKU with the largest surface area determines the basic shape of the outer packaging. Since the dimensions and weight of each item are known, the system selects and suggests the appropriate carton. In rare cases, it may still be necessary to select a different outer packaging, the employee then changes this accordingly and selects a suitable alternative. The outer packaging is also inventory-managed. Accompanying documents (e.g. proforma invoice, etc.), especially for export, are also printed out and enclosed with the shipment. All items are thus packed into the outer packaging, provided with further packaging material to protect the contents, the shipment is sealed and ready for dispatch.