Fulfillment Wissen
Pick & Pack – Kernelement des Fulfillment
Kaum ein Element des modernen Fulfillment hat eine solche Bedeutung wie der Pick & Pack-Prozess. Hocheffiziente, IT-gestützte Prozesse begleiten den Menschen bei der täglichen Arbeit. Trotzdem ist der Faktor Mensch ein wesentlicher Bestandteil dieses Prozesses. Die IT-Unterstützung erhöht die Effizienz massiv und schließ gleichzeitig Fehlerquellen aus.
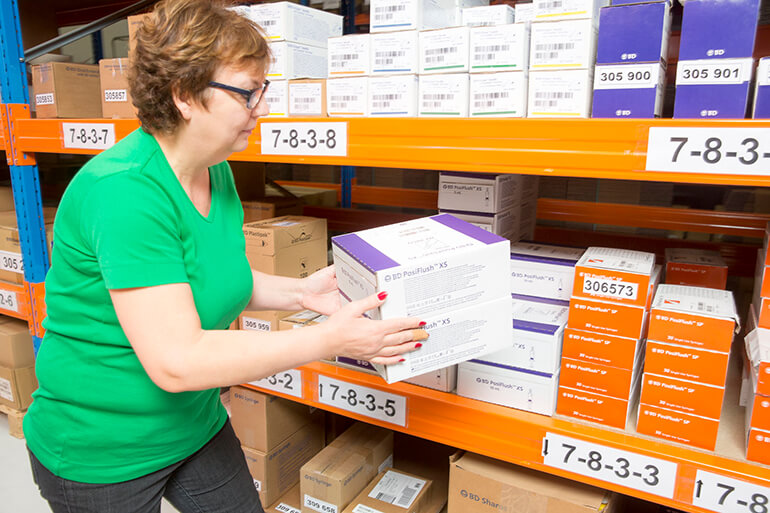
Pick & Pack ist sozusagen das Herzstück des Fulfillments
Pick Jeder eingegangene Versandauftragt erzeugt einen Lieferschein (der der Sendung beigelegt wird) oder einen Kommissionierschein, wenn die Sendung ohne Lieferschein ausgeliefert wird. Auf dem jeweiligen Beleg ist die Lieferscheinnummer als Barcode enthalten. Grundsätzlich gibt es also immer ein Dokument mit aufgedrucktem Barcode. In unserem Fall sieht dies z.B. so aus. Lieferscheinnummer: 322-04711893.
Zentrales Element des Pick-Vorgangs sind zwei Komponenten:
-
Wegeoptimierung: Die Warenwirtschaft weiß immer ganz genau, wo sich welcher Artikel befindet. Also auf welchem Lagerstellplatz oder Fachboden. Bei der Wegeoptimierung wird ein möglichst geringer bzw. der optimale Laufweg von einem zum nächsten Kommissionierteil, also Artikel (SKU) angestrebt. Das „Traveling Salesman Problem“, auf Deutsch „Problem des Handlungsreisenden“, ist ein klassisches Problem in der Theorie der Wegeoptimierung. Es basiert auf der Annahme, dass verschiedene Zielpunkte bei minimaler Zeitspanne innerhalb eines Zyklus nur einmal erreicht werden sollen. Zur Lösung dieses Problems können die Weglängen aller möglichen Laufwege berechnet und dann die mit der kleinsten Weglänge, unter Berücksichtigung der zur Verfügung stehenden Ressourcen, ausgewählt werden.
-
Umlagerung: Ein ganz praktisches Problem. Artikel, also SKU’s, die oft gebraucht werden, sollen in einem Hochregallager an den griffbereiten Stellen, als bis zu zwei Meter erreichbar. Sein, damit das Personal möglichst schnell den Pickvorgang durchführen kann. Dabei analysiert die Warenwirtschaft permanent den Artikelabfluss und liefert dem Lagerpersonal wichtige Tipps zum Umlagern von Artikel aus höheren Lagerregionen in Regionen, die dem Pic-Personal direkt zugänglich ist. Geht also beispielsweise ein Artikel aufgrund saisonaler Aspekte mehr als zu einem früheren Zeitpunkt, werden die Mitarbeiter angehalten, diesen Artikel griffbereit zu lagern. Andere Artikel können aufgrund geringeren Abflusses wieder oben im Hochregallager eingelagert werden. Die Herausforderung des Algorithmus besteht darin zu erkennen, ob dies kurzfristige Effekte sind, die zu diesem Materialabfluss führen (z.B. Messen), oder ob dies längerfristige Aspekte, wie es eben saisonale Effekte sind.
& Pack Die einzelnen Komponenten (Positionen) des Auftrags werden am Point-of-Pack (PoP) in eine geeignete Umverpackung eingebracht wird. Die geeignete Umverpackung wird vom Warenwirtschaftssystem dem Mitarbeiter vorgeschlagen. Durch die Geo-Daten-Erfassung beim Wareneingang sind sämtliche Informationen des Auftrags und dessen Inhalt verfügbar. Die SKU mit dem größten Flächenmaß bestimmt die Grundform der Umverpackung. Da Maße und Gewicht eines jeden Artikels bekannt sind, wählt das System den passenden Karton aus und schlägt ihn vor. In selten Fällen kann es trotzdem sein, dass eine andere Umverpackung gewählt werden muss, dies ändert der Mitarbeiter dann entsprechend und wählt eine passende Alternative. Auch die Umverpackung ist bestandsgeführt. Warenbegleitdokumente (z.B. Proforma-Rechnung, etc.), insbesondere für den Export werden ebenfalls ausgedruckt und der Sendung beigelegt. Alle Positionen werden so in die Umverpackung gepackt, mit weiterem Verpackungsmaterial zum Schutz des Inhalts versehen, die Sendung verschlossen und für den Versand fertig.